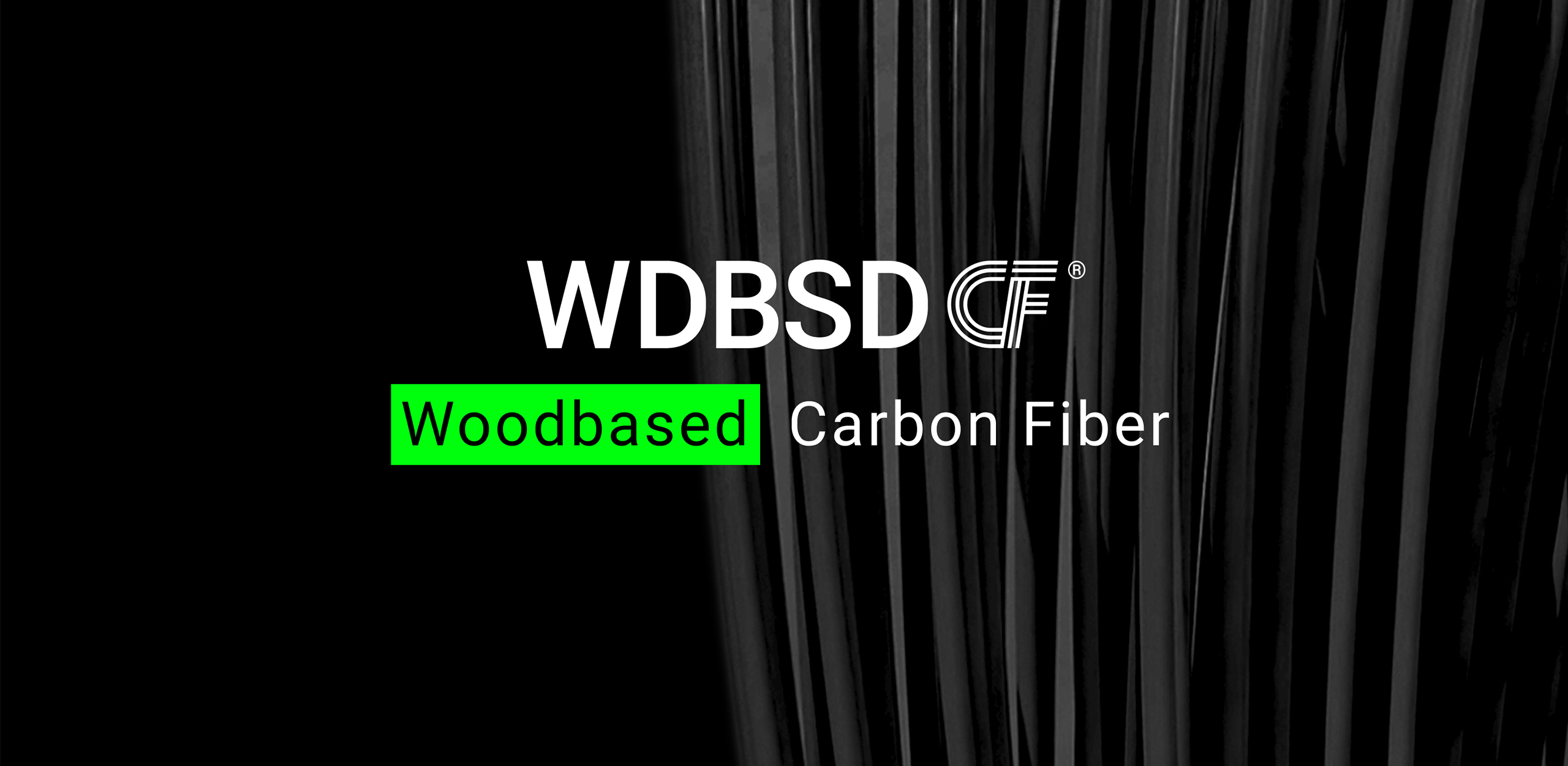
The next generation of carbon fibers – engineered to meet your industry’s demands.
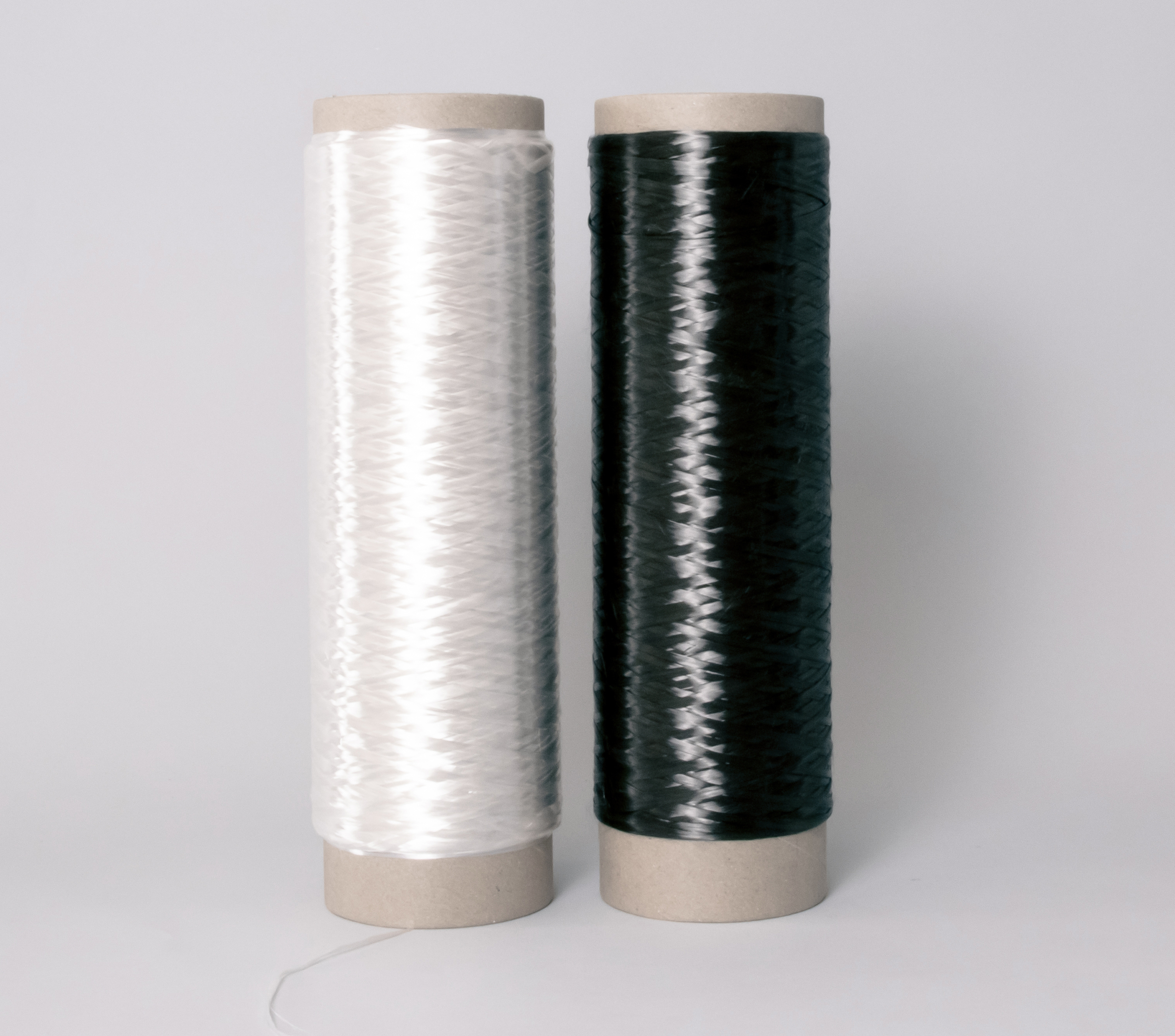
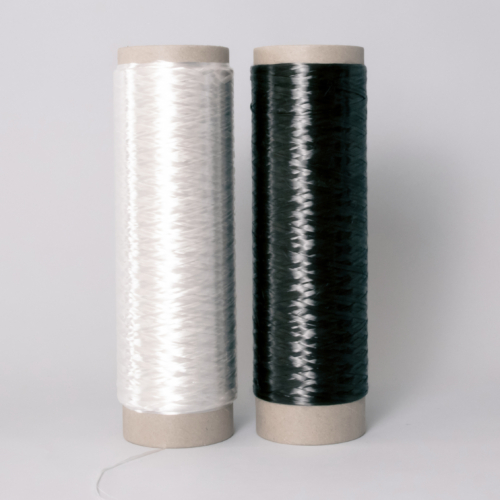
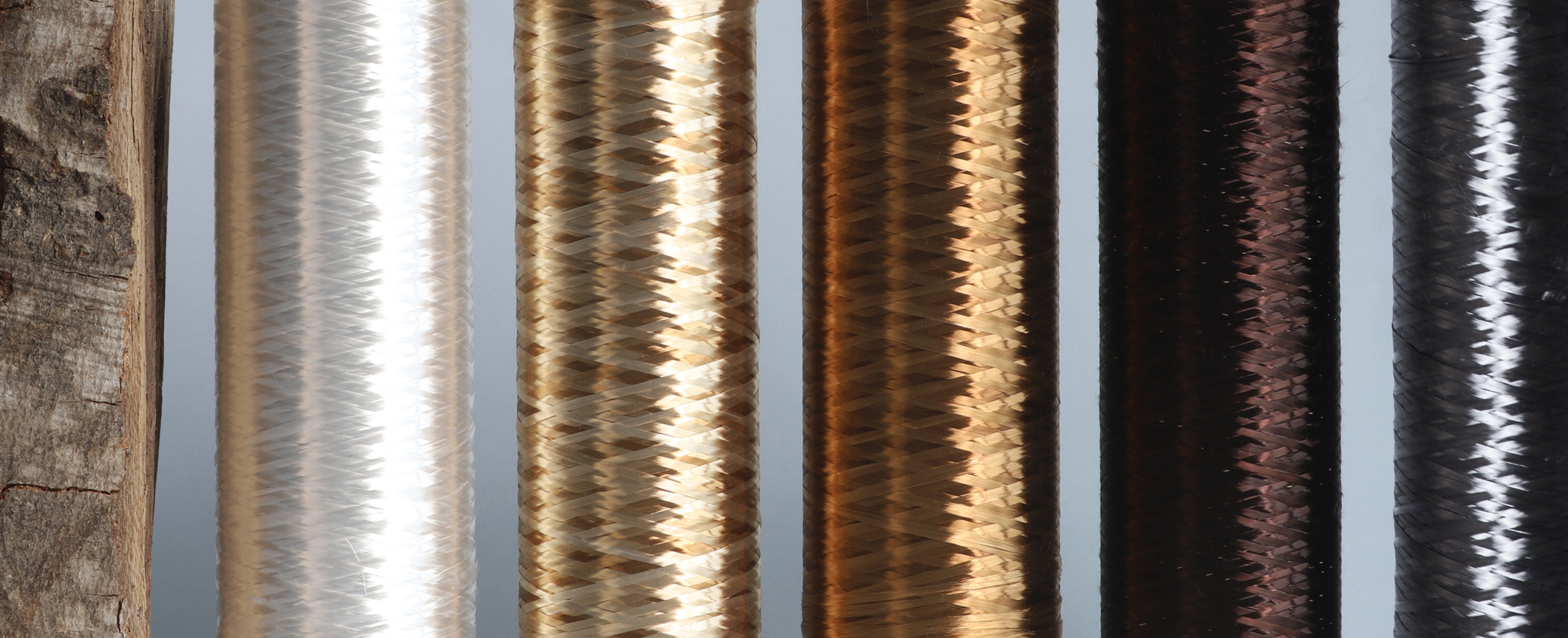
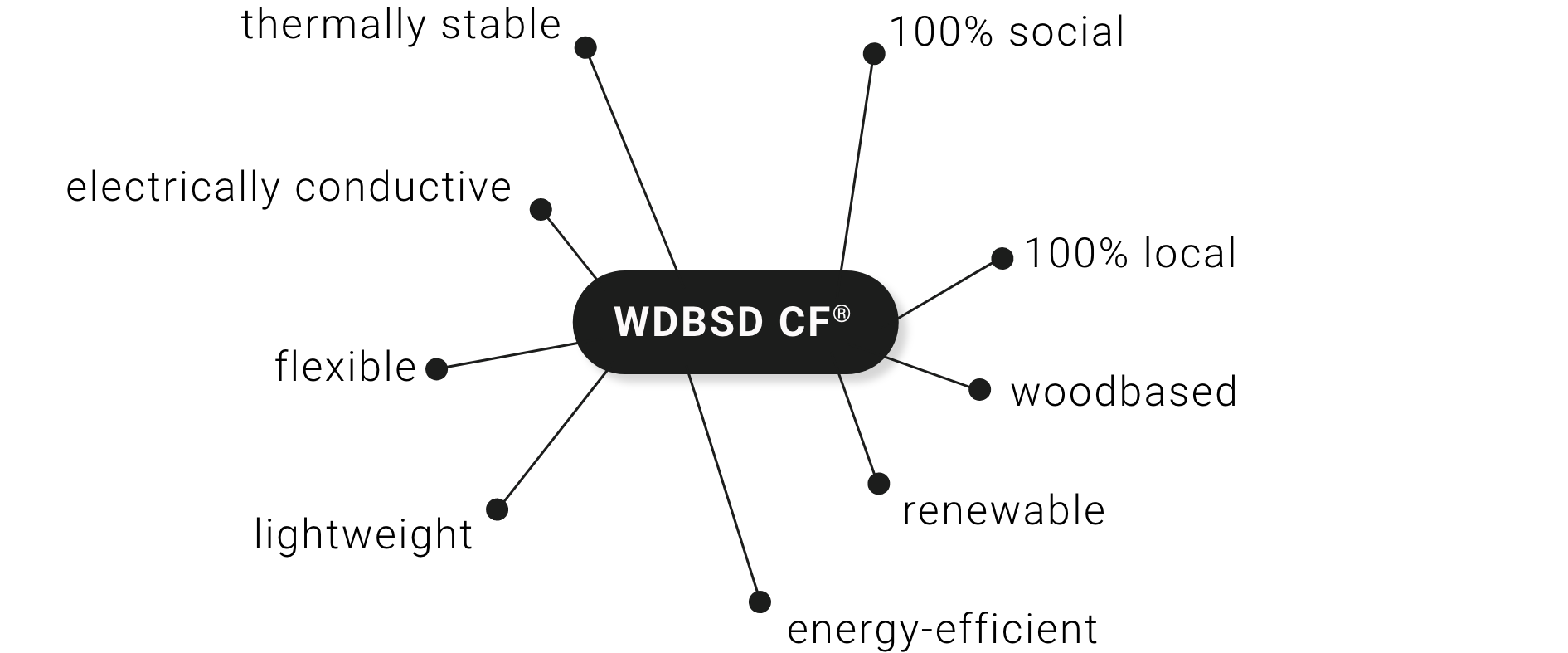
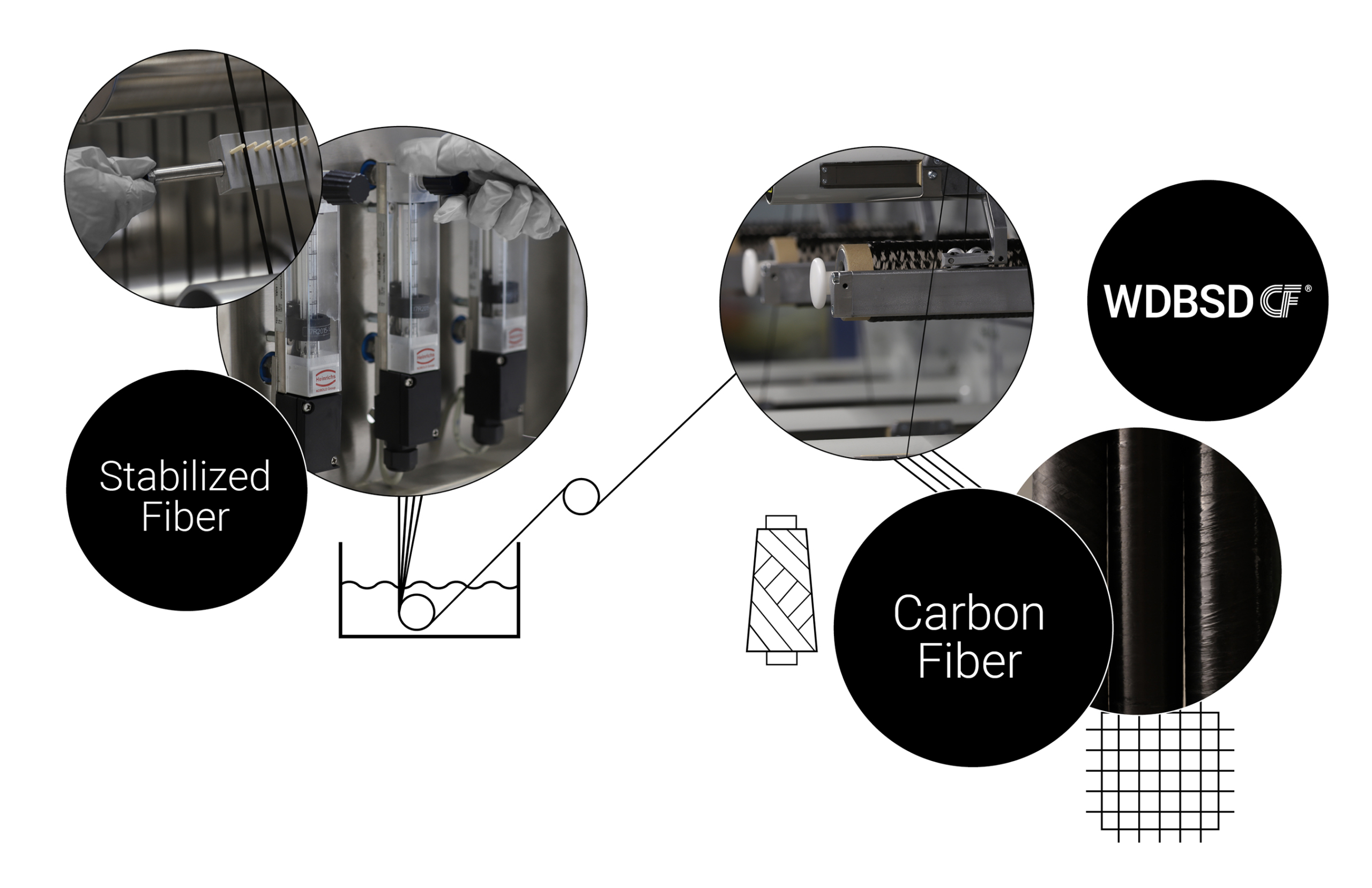
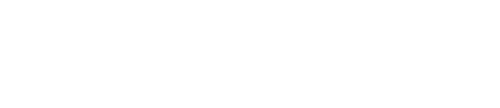
WDBSD CF opens up a broad range of potential applications and delivers exceptional performance across multiple industries. From enhancing everyday products to revolutionizing high-performance systems, its unique combination of sustainability, strength, and versatility makes it an ideal material for a variety of technical and consumer uses.
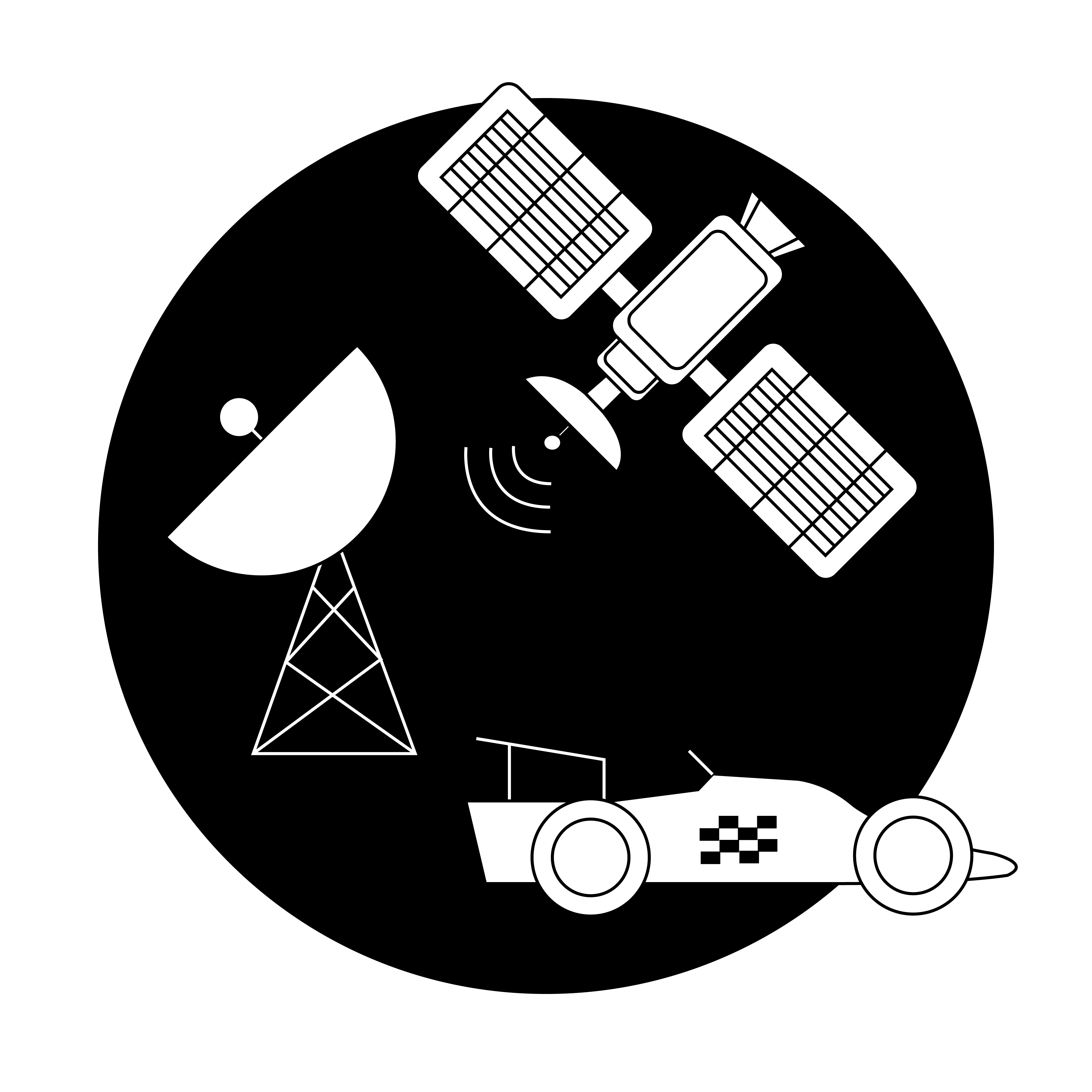
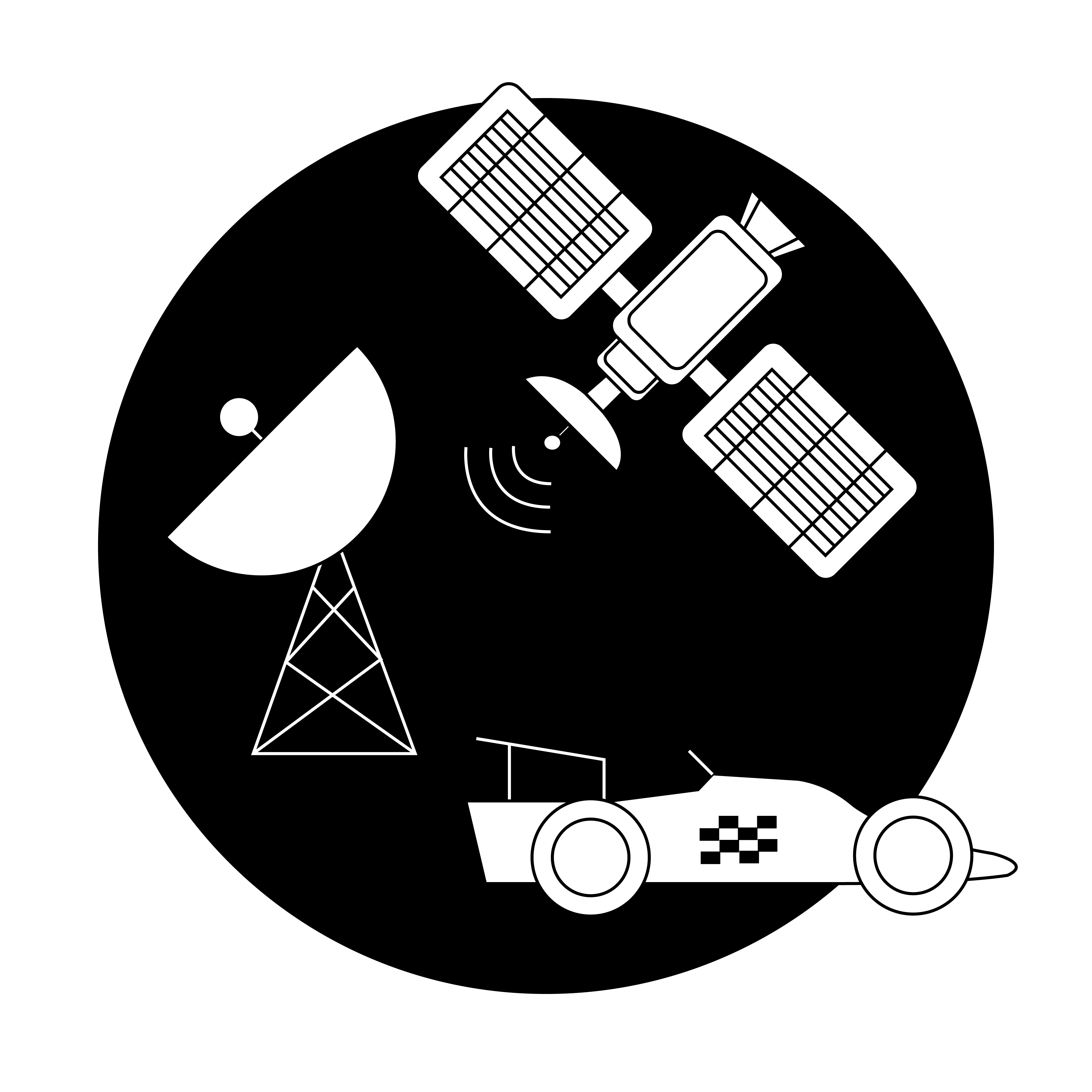
Reach out to our fiber technology specialists and learn more about the properties of WDBSD CF.
The production process of WDBSD CF reflects a shift toward greater sustainability and efficiency, offering an alternative to the conventional, resource-intensive production of PAN-based carbon fibers.
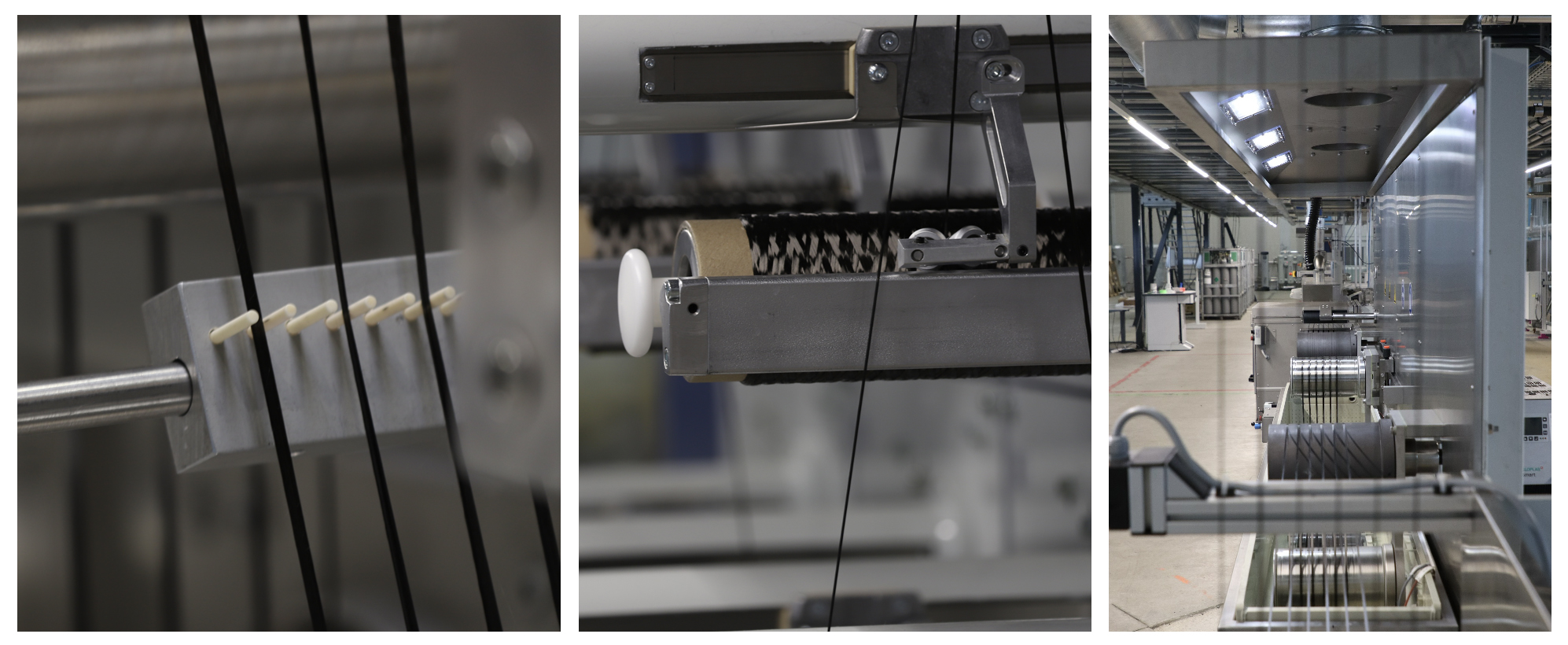
PAN-Based Carbon Fibers:
A Resource-Intensive Process
Energy-Intensive Production
The production of PAN fibers includes stabilization at 200-300 °C, carbonization at 1,000-2,000 °C and, depending on the end application, graphitization at temperatures above 2,500 °C – these processes require large amounts of energy over extended periods of time.
Environmental Impact
The reliance on acrylonitrile, a petrochemical derivative, contributes to the environmental impact, not only through energy consumption in manufacturing, but also through the release of harmful gases, requiring extensive exhaust gas treatments.
Complex Waste Management
The PAN-based process often results in waste by-products that need complex disposal or recycling processes.
WDBSD CF®:
A Shift to Wood-Based Carbon Fibers
Energy-Efficient Production
The WDBSD CF process is optimized to reduce energy consumption at key stages. By using lower temperatures and more efficient processes, we significantly reduce the energy required for stabilization. The use of direct spinning techniques for cellulose fibers further reduces operational costs and environmental impact.
Renewable and Local Resources
Our raw material, cellulose from regional hardwood, is both abundant and renewable. This reduces reliance on non-renewable, fossil-based sources, creating a more sustainable supply chain
Fewer Harmful By-Products
Cellulose-based carbon fibers do not emit the same level of harmful gases during production, removing the need for complex exhaust treatments. This ensures a cleaner, more environmentally friendly production cycle.
PAN-Based Carbon Fibers: A Resource-Intensive Process
Energy-Intensive Production
The production of PAN fibers includes stabilization at 200-300 °C, carbonization at 1,000-2,000 °C and, depending on the end application, graphitization at temperatures above 2,500 °C – these processes require large amounts of energy over extended periods of time.
Environmental Impact
The reliance on acrylonitrile, a petrochemical derivative, contributes to the environmental impact, not only through energy consumption in manufacturing, but also through the release of harmful gases, requiring extensive exhaust gas treatments.
Complex Waste Management
The PAN-based process often results in waste by-products that need complex disposal or recycling processes.
WDBSD CF®: A Shift to Wood-Based Carbon Fibers
Energy-Efficient Production
The WDBSD CF process is optimized to reduce energy consumption at key stages. By using lower temperatures and more efficient processes, we significantly reduce the energy required for stabilization. The use of direct spinning techniques for cellulose fibers further reduces operational costs and environmental impact.
Renewable and Local Resources
Our raw material, cellulose from regional hardwood, is both abundant and renewable. This reduces reliance on non-renewable, fossil-based sources, creating a more sustainable supply chain
Fewer Harmful By-Products
Cellulose-based carbon fibers do not emit the same level of harmful gases during production, removing the need for complex exhaust treatments. This ensures a cleaner, more environmentally friendly production cycle.
WDBSD TX®
A sustainable precursor fiber for high-performance applications across various industries.
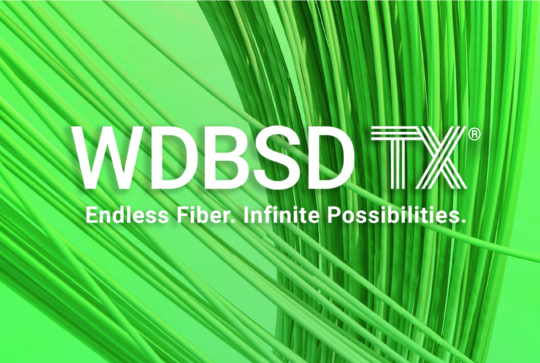
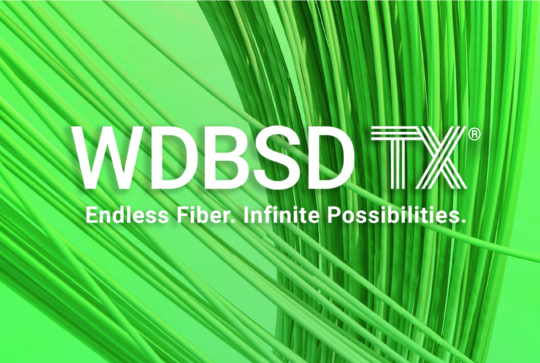
WDBSD TX®